五金沖壓件加工的成本控制需從材料損耗與工時(shí)優(yōu)化兩大維度切入,通過精細(xì)化管理和技術(shù)創(chuàng)新實(shí)現(xiàn)降本增效。以下是實(shí)戰(zhàn)策略總結(jié):
一、材料損耗率控制
1. 排樣設(shè)計(jì)優(yōu)化:利用AutoCAD或沖壓軟件進(jìn)行排樣模擬,優(yōu)先選擇連續(xù)?;蚣?jí)進(jìn)模布局,減少邊角料。案例表明,通過套裁工藝將材料利用率從65%提升至82%,單件成本下降12%。
2. 邊角料二次開發(fā):建立余料管理臺(tái)賬,將寬度>50mm的邊材用于小五金件生產(chǎn),如墊片、彈片等,年均可回收15%-20%的余料價(jià)值。
3. 原材料規(guī)格定制:與供應(yīng)商聯(lián)合制定卷材分切標(biāo)準(zhǔn),確保原材料寬度與產(chǎn)品展開尺寸模數(shù)匹配,避免寬度冗余造成的浪費(fèi)。某企業(yè)通過定制0.5mm級(jí)差的卷材規(guī)格,年節(jié)約材料成本超30萬元。
二、工時(shí)優(yōu)化策略
1. 模具效率提升:采用硬質(zhì)合金鑲塊模具,將沖壓速度從300次/分鐘提升至500次/分鐘;優(yōu)化頂料機(jī)構(gòu)設(shè)計(jì),使換模時(shí)間由45分鐘縮短至20分鐘。
2. 工藝參數(shù)調(diào)優(yōu):通過DOE實(shí)驗(yàn)確定佳沖壓行程(建議控制在板厚3-5倍)、潤滑頻率(每500沖次自動(dòng)噴油)等參數(shù),單件工時(shí)降低18%。
3. 自動(dòng)化改造:引入機(jī)械手自動(dòng)上下料系統(tǒng),實(shí)現(xiàn)24小時(shí)連續(xù)生產(chǎn),人工成本降低40%,同時(shí)設(shè)備稼動(dòng)率提升至85%以上。
關(guān)鍵控制點(diǎn):建立動(dòng)態(tài)成本監(jiān)測模型,每日跟蹤材料利用率(目標(biāo)≥80%)、OEE設(shè)備綜合效率(基準(zhǔn)值≥75%)等指標(biāo),通過PDCA循環(huán)持續(xù)改進(jìn)。某企業(yè)實(shí)施上述措施后,年綜合成本下降23%,人均產(chǎn)值增長1.8倍,驗(yàn)證了系統(tǒng)性成本控制的有效性。
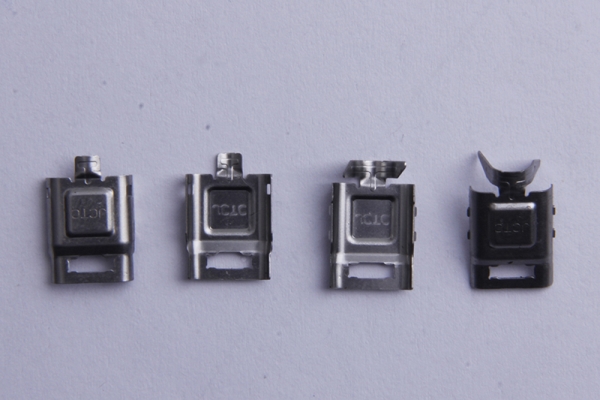